
Joining and bonding
Five steps are taken to develop reliable bonding and welding processes: application requirements, material selection, product design, bonding/welding process selection and equipment needs. By considering these five stages of development, effective and reliable solutions are created for specific applications. Make use of Etteplan’ s know-how and experience as a competitive advantage. By providing expert advice on your application, we can optimize your processes quickly and efficient
Joining and bonding: process selection and design
Determining the best process for bonding and joining can be a challenge, given the multitude of options available. The selection process heavily relies on the application requirements and materials involved. Adhesive bonding may be the ideal solution for some cases, while thermal compression bonding or welding may yield better performance in others.
Based on your specific application requirements and materials, our experts can recommend the most suitable process for your needs.
Material selection
At Etteplan, we understand that material selection is crucial in bonding and welding operations. Our team of material science experts will assist you in selecting the right process and materials to ensure success. We consider all product requirements such as strength, application temperature, corrosion resistance, and electrical properties to make informed decisions.
Equipment and process modules
Once the process design and product design are finalized, we help you select suitable equipment and process modules to optimize your bonding process. Our versatile machine platform includes various motion systems (axis, robot, cobot) and process modules like dispensing modules, thermal compression modules, laser welding modules, resistance welding modules, among others.
Application requirements
We assess bonds or welds based on functional, performance, and visual criteria during the initial design phase. This allows us to incorporate specific bonding features seamlessly. We determine initial requirements for strength, fatigue life, environment considerations, and electrical performance.
In addition to that, our experienced team helps with part design in line with the chosen bonding process and materials. Each bonding method has specific design rules that enhance reliability. For example, in adhesive bonding, a well-designed gap between parts acts as either a capillary fill or stress relief when there is a mismatch in the Coefficient of Thermal Expansion (CTE).
With Etteplan's support in product design, you can develop robust and reliable bonding and joining processes, giving you an edge in design for manufacturing.
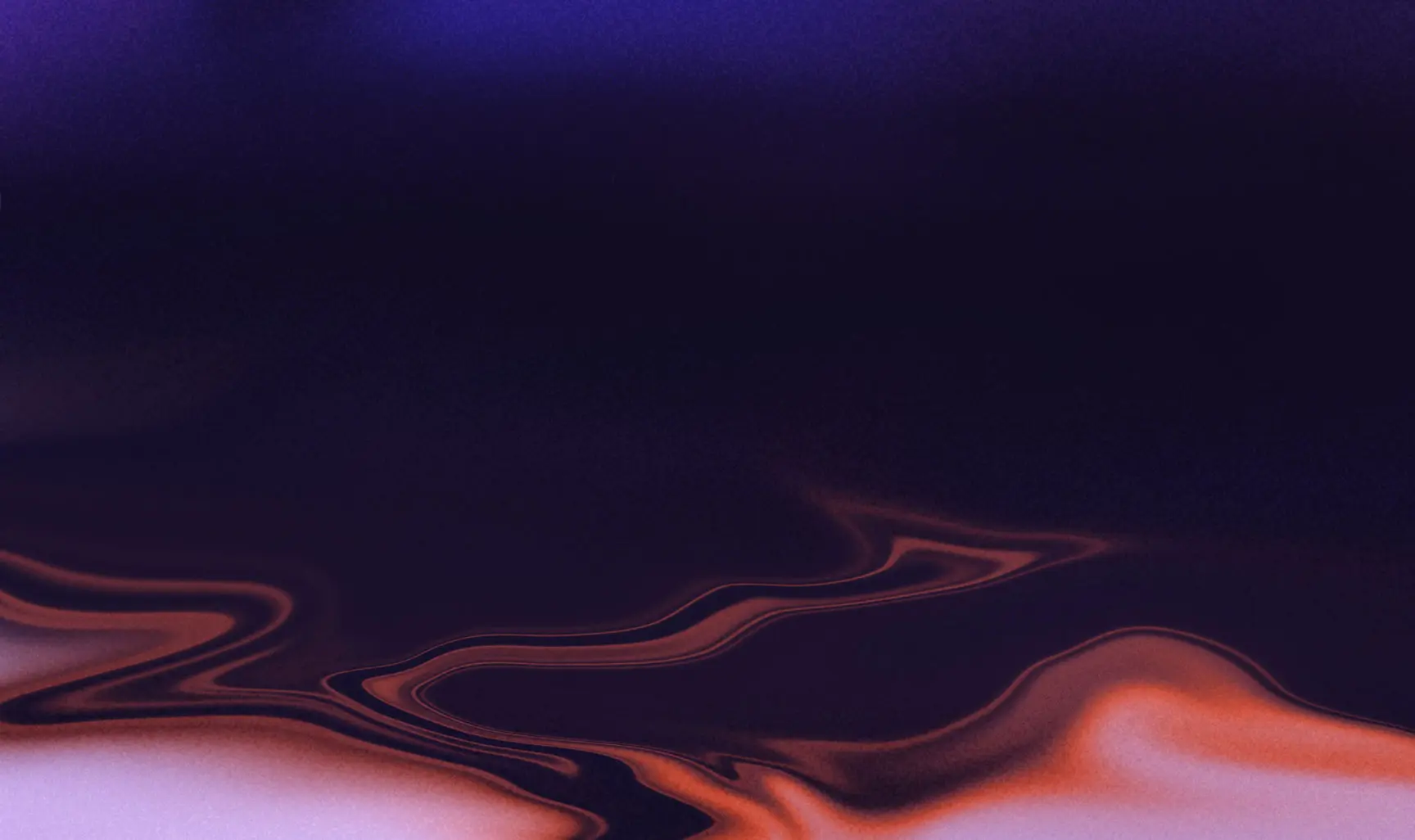
Ask our expert a question

Vice President, Etteplan Production Solutions and Country Manager, the Netherlands
Mandatory field
When you submit this form, our specialist will be in touch with you by email or telephone. By submitting the form you accept our privacy statement.