
Optimization of Assembly Processes: Improved Efficiency and Quality in One
Are you experiencing that your assembly processes are not running as smoothly as you would like? Perhaps you see that your team is working harder, but the results are lagging. Does this sound recognizable? Many companies face similar challenges and are looking for ways to improve their processes. At Etteplan, we understand this and are here to support you.
The challenges of assembly
Inefficient processes can negatively affect the productivity and quality of your assembly. Perhaps cooperation between employees and machines is not working optimally, or there is a need for more flexibility to respond to changing market demands.
These are the eight most common assembly problems:
Quality level below standard, quality costs rise
Product life cycle gets shorter
Price pressure from low-wage countries
Product variety increases
Rapid fluctuation or shortage of production personnel
Productivity loss due to inefficiency (8 wastes)
Increasing fluctuations in market demand
Long lead time between production and market
Do you recognize one or more of these challenges for your assembly process? If so, there may be opportunities for optimization and it's time for a fresh look at your assembly processes.
Our approach: step by step to improvement
At Etteplan, we have developed a structured approach to optimizing assembly processes. We combine - where necessary - manual and automated techniques in a way that suits your organization. This is our roadmap:
Product and Process Analysis
We start with a comprehensive analysis of the current situation. What works well and where are the bottlenecks? This insight is essential for determining the right improvements.
Outline design
Based on our findings, we develop a clear plan. We look at material flow and the cooperation between employees and machines, so that we lay a solid foundation for optimization.
Detailed design
In this phase, we elaborate on the solutions. This may mean redesigning the production line or applying automation to specific process steps. We make sure the solutions fit your specific needs.
Realization and Validation
Now it is time to put the plans into practice. We implement the solutions and monitor the results together. We ensure that the improvements actually lead to higher efficiency and quality.
Maximize your productivity through more efficient processes, achieve flawless quality for higher customer satisfaction, and benefit from optimal flexibility that allows you to respond quickly to changing market conditions. This combination ensures that your production is not only more effective, but also future-proof.

Significant improvement in assembly with LCIA

The Five Biggest Challenges in Assembly Processes and How to Recognize Them

Optimize your product development with digital twins
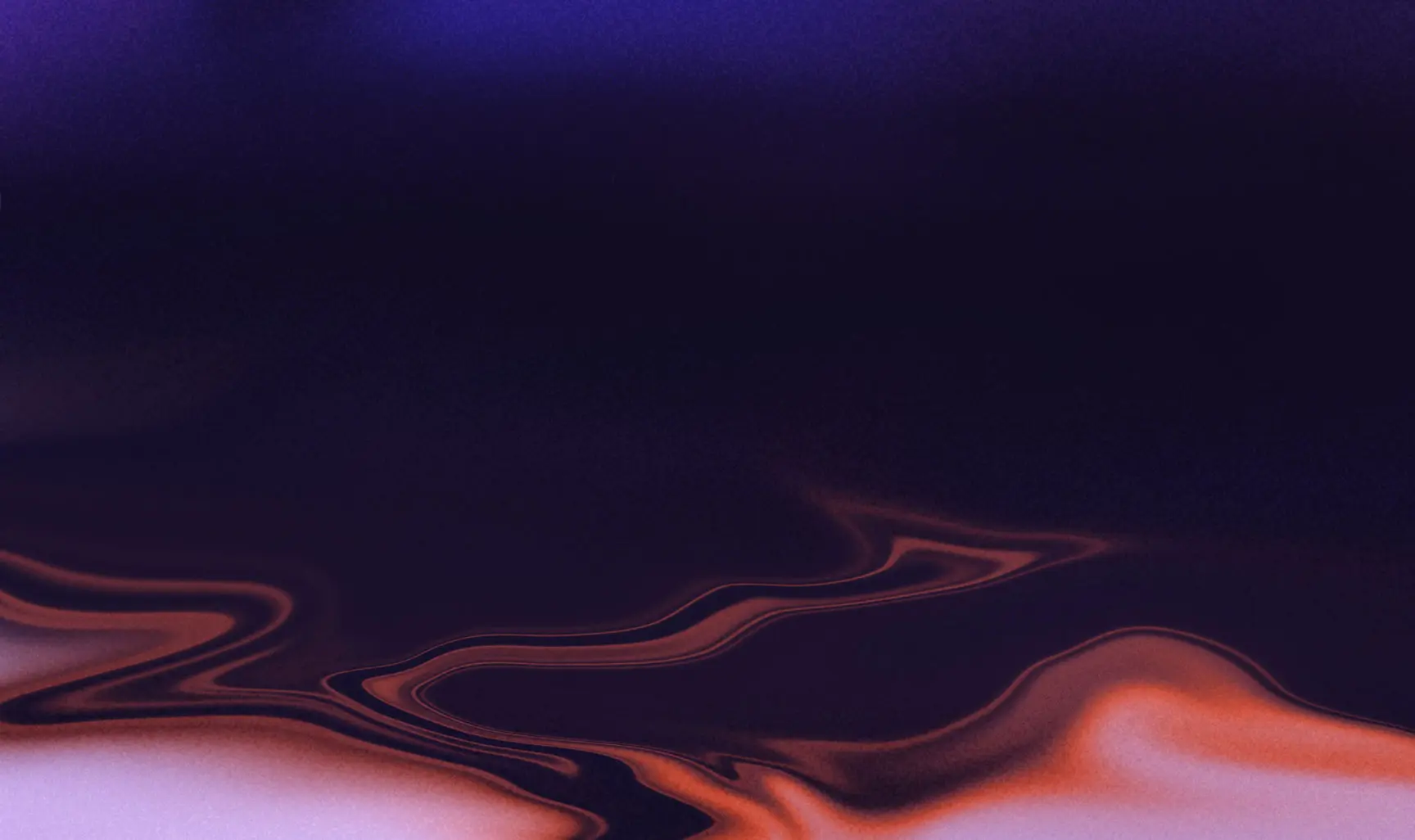
Ask our expert a question

Vice President, Etteplan Production Solutions and Country Manager, the Netherlands
Mandatory field
When you submit this form, our specialist will be in touch with you by email or telephone. By submitting the form you accept our privacy statement.