
UPCAST® enhances cooling performance of copper rod drawing machine with AM technology
UPCAST® is the leading supplier of upward continuous casting technology for a wide range of non-ferrous applications. UPCAST® casting lines are reliable and cost effective, and the process allows you to cast different rod or tube sizes simultaneously.
The process works by submerging casting coolers in molten copper, which is forced upwards by metollastatic pressure and solidifies in the cooler. After solidification, the rod/tube is controlled by a high-precision automated servo system and directed to the coilers. Cooling performance is one of the key factors in rod and tube quality and productivity.
Customer challenge
The UPCAST® engineering team started to look for novel ways to meet demand for increased speed and better surface quality of the copper rods. UPCAST® wanted to improve cooling performance in their casting machine by optimizing the flow pattern and reducing the pressure drop. The company had ideated and verified via CFD simulations some concepts for better flow and improved cooling, but they needed a reliable and new way to implement them.
Solution
UPCAST® contacted Etteplan, a leading engineering and design company that specializes in additive manufacturing (AM) solutions. Etteplan analyzed the cooling system and the CFD results, and designed a new additive manufactured part that would enhance the cooling performance. The new part had an optimal flow pattern that ensured uniform and laminar cooling water distribution, as well as reduced pressure drop. The part was also designed to be compatible with several AM materials, such as stainless steel and copper alloys, depending on the customer's preference.
Benefits
- Improved flow and reduced pressure drop of the cooling media, which improved the cooling efficiency and the final product quality
- Better looking appearance of the component, which enhanced the visual appeal and the brand image of the UPCAST® machines
- More flexibility and versatility in the material selection and properties, which was enabled by the use of different LPBF materials for different applications and environments
- More cost-effective and faster production process, which reduced the lead time and the inventory costs of the component during prototype phase
In addition, Etteplan educated UPCAST's engineers about AM technologies during the project, and provided them with support. This helped UPCAST® to understand and adopt the AM technology, and to leverage its potential for their future product development and innovation.
Related reference cases
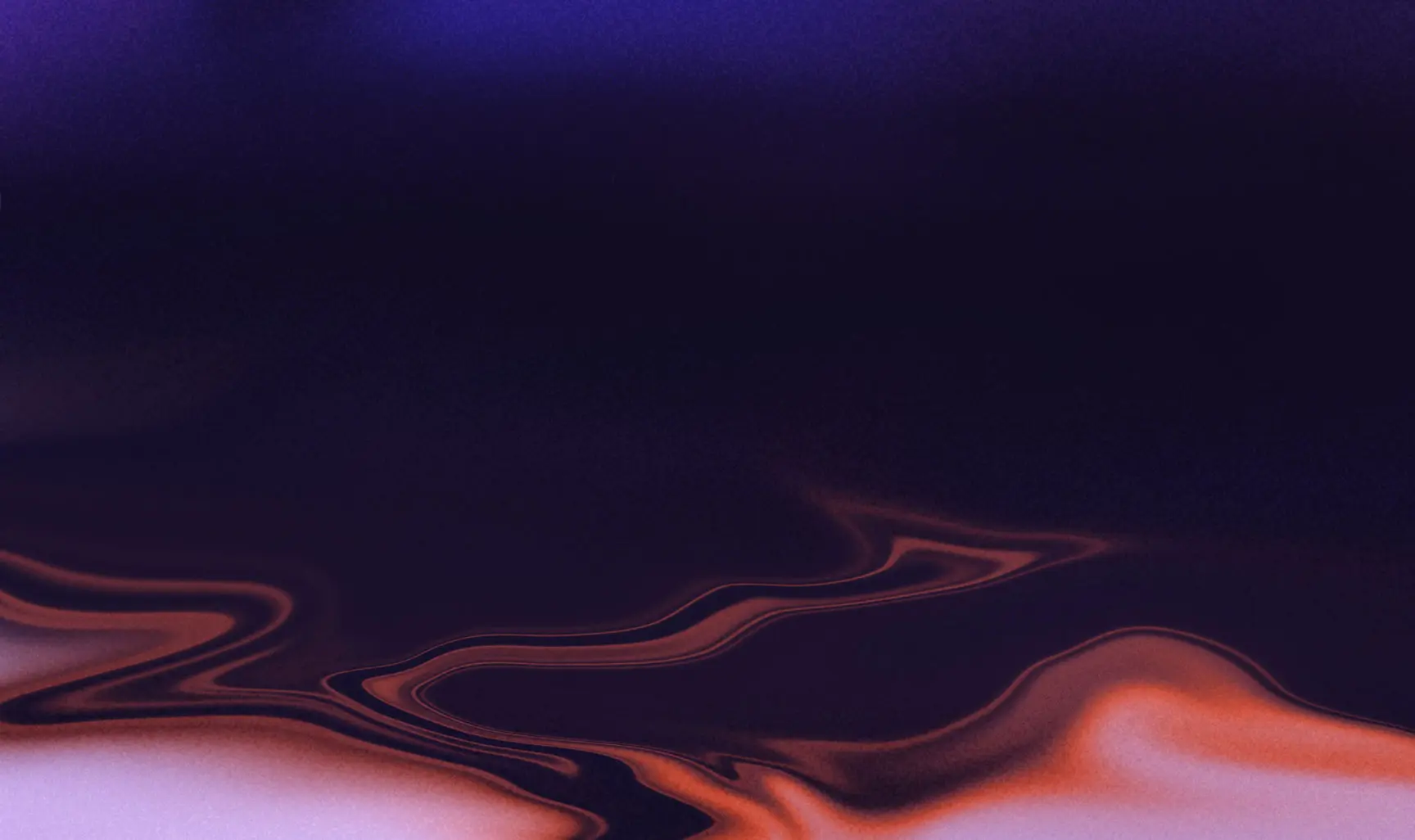
Ask our expert a question

Department Manager, AMO
Mandatory field
When you submit this form, our specialist will be in touch with you by email or telephone. By submitting the form you accept our privacy statement.