
Senop harnesses additive manufacturing for developing a unique solution
Senop, a trusted provider of advanced optonics and critical communication solutions for the defence and industrial markets, was seeking a solution for a transportation fastening device that would prevent component movement during repeated transports. Etteplan, leveraging additive manufacturing expertise, utilized the laser powder bed fusion method to create a solution. Additive manufacturing allowed for cost-effective production and added value for end-users.
Unable to display the content
The cookies you have selected prevent this content from being displayed. To view content, you must accept marketing cookies.
A solutions for component security during transports
Senop faced a challenge in their product, which required the creation of a transportation fastening device. The primary objective was to prevent component movement during repeated transports. Furthermore, the fastening device needed to be easily operable by hand, without the need for any tools. As there was no previous solution to this challenge, it required the development of a completely new product.
“Senop had earlier good experience co-operation with Etteplan. So it was easy to operate with a known partner with proven expertise in different fields of engineering.”
Juha Tolppa
Project Manager at Senop
Another challenge Senop faced was the limited space available for the fastening and installation process. Additionally, the fastening needed to be performed and dismantled within a few seconds. The presence of loose parts was not allowed to prevent individual pieces from being lost during the product's lifecycle.
Senop partners with Etteplan to harness additive manufacturing
Senop was interested in exploring the possibilities of additive manufacturing and wanted to leverage Etteplan's expertise in finding a solution to their problem. Together, the partners identified the potential of utilizing the laser powder bed fusion method for polymers. This method offered advantages in terms of design freedom and a wide range of material options.
Through collaborative discussions and brainstorming, a concept for a mechanism was developed. The objective was to create a solution where a single thumb movement could produce both the fastening motion and force, resembling a ratchet structure for locking and unlocking.
Optimal functionality with laser powder bed fusion
The resulting solution utilized the the polymer laser powder bed fusion method to manufacture the fastening device. The process allowed for the creation of complex geometries with high dimensional accuracy, ensuring the functionality of the mechanism. In taking advantage of these possibilities, a compliant mechanism was utilized in the ratchet structure for locking and unlocking. To streamline the manufacturing process, the individual moving parts were printed in their final positions within the component. This integrated manufacturing approach eliminated the need for a separate assembly phase.
During the implementation phase, the functionality of the product was fine-tuned through multiple iteration rounds. This iterative process allowed for adjustments to be made, ensuring the product met Senop's requirements. The printing partner, 3D Formtech, played a crucial role in this phase, demonstrating their commitment to delivering a fully functional and production-ready product.
A customized solutions delivers value for Senop and end-users
The final product, a transportation fastening device, successfully addressed Senop's challenges. The device provided a secure fastening mechanism, preventing component movement during transportation. Its hand-operable design allowed for easy and tool-free operation, making it efficient and convenient for users.
“On Senop’s side, offering design and development services to our customer was a new opportunity for the long-term customer relationship that had only focused on manufacturing and subcontracting . From our point of view, this was a good opportunity to patch the lack of R&D resources to create the design."
Juha Tolppa
Project Manager at Senop
By embracing additive manufacturing methods, Senop was able to overcome previous limitations and achieve a solution that was not possible with traditional manufacturing techniques. The utilization of additive manufacturing, especially in polymer printing, enabled the cost-effective production of individual mechanical components and complete mechanisms in small series production. This approach not only delivered tangible benefits to Senop but also provided added value to the end-users of their products.
Related reference cases
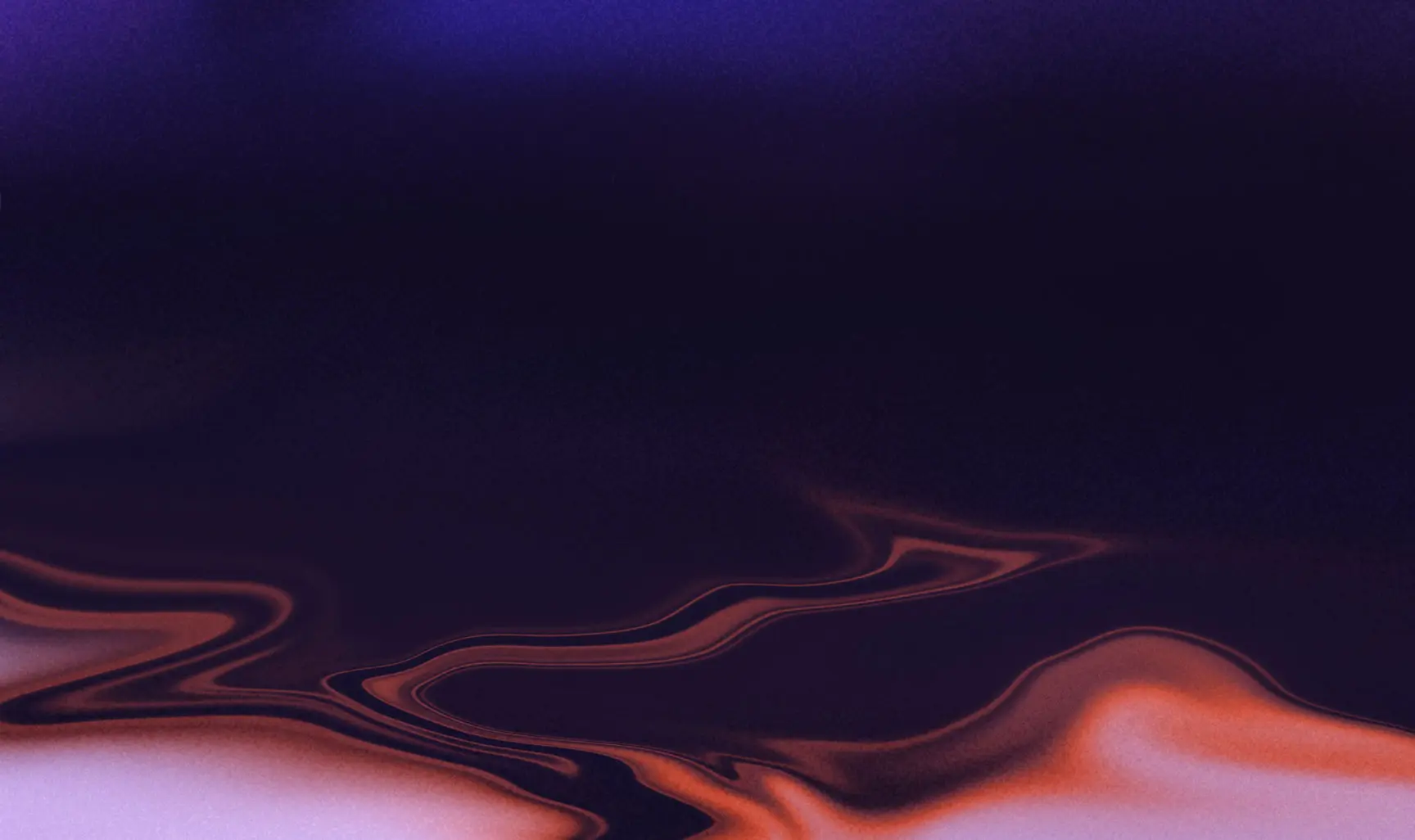
Ask our expert a question

Department Manager, AMO
Mandatory field
When you submit this form, our specialist will be in touch with you by email or telephone. By submitting the form you accept our privacy statement.