Helping Schaeffler guarantee product quality through testing
As a leading global supplier to the automotive and industrial sectors, the Schaeffler Group has been driving forward groundbreaking inventions and developments in the fields of motion and mobility for over 70 years. With innovative technologies, products, and services for CO₂-efficient drives, electric mobility, Industry 4.0, digitalization, and renewable energies, the company is a reliable partner for making motion and mobility more efficient, intelligent, and sustainable. The technology company manufactures high-precision components and systems for powertrain and chassis applications as well as rolling and plain bearing solutions for a large number of industrial applications.
Condition monitoring can be expensive. Which is why up to 95% of all machines inside factories are only sporadically monitored, or often not at all. This can lead to unplanned breakdowns and downtime. To remedy this, Schaeffler has launched their new condition monitoring system: OPTIME. The new system allows for comprehensive condition monitoring that is both easy and affordable. Thanks to its simple plug & play installation, OPTIME allows you to start monitoring hundreds of rotating machines in just a few hours. It can detect potential damage, imbalances or misalignments even weeks in advance. This enables the operator to easily and conveniently plan their long-term maintenance, manpower or spare-parts requirements.
Schaeffler wanted to ensure that the product’s quality was according to their high standards. To guarantee this, the project required a modern and an agile testing process. Etteplan was the choice since we had the capabilities to effectively deliver the schedule and scope of the project which were paramount to the customer. Additionally, we were able to provide a wide range of services and competences that Schaeffler would require during the product development project.
Test planning, System Integration Testing and End to end testing
The planning started with workshops where customer requirements and needs were converted to actual work backlog. The planning phase also included ensuring that the testing was robust and the choice of tools were suitable for the project. Moreover, the project’s scope which included system integration testing and end to end testing in addition to creating simulations of the product’s key hardware parts, was agreed on.
Next, end to end testing was conducted as automated testing with the Robot Framework from web and mobile UIs and through the REST interface. End to end testing was supported with manually created system simulations, which allowed for faster and more comprehensive testing of the whole product. In addition to using real HW products in testing, creating a simulation for HW related projects enabled the end to end testing to be executed daily thus allowing Schaeffler to get more frequent and reliable results from the testing.
Furthermore, System Integration Testing was applied to the parts where the system required it. System Integration was done through automation with Robot Framework from web UI, mobile UI and from interface level.
Additionally, Etteplan delivered testing consultation in other areas including environmental testing. Etteplan guided the project and development from the quality perspective. Essentially this meant that Etteplan’s experts ensured that the physical product functioned and endured as expected in its’ operating environment and that requirements were met. Etteplan also helped with environmental test design and with interpreting test results.
Lastly, Etteplan trained Schaeffler’s testing team and one of their partner’s teams to continue testing and test development.
“Altogether, the implementation went very well and co-operation will continue in the future. In fact, we have already moved into new projects with Schaeffler,” commented Timo Kallinen, Head of Product Verification, Etteplan.
“We have been pleased with Etteplan’s ability to provide us just the right competences for our testing needs and just on time.”
Jarno Suomela
Vice President Solutions Business Development at Schaeffler
Etteplan is the one-stop-shop for engineering
Daily testing rounds allowed Schaeffler to get more frequent and reliable results while guaranteeing the quality of the product. The fast schedule that Etteplan was able to carry out surprised the customer as did the range of services Etteplan provided. Schaeffler benefitted immensely from the broad expertise of Etteplan. The project compassed different areas of engineering expertise, not just in testing but also in plastic chemistry, batteries, radio frequency etc. Due to Etteplan’s capabilities, Schaeffler’s time to market with OPTIME was significantly shortened.
Related reference cases
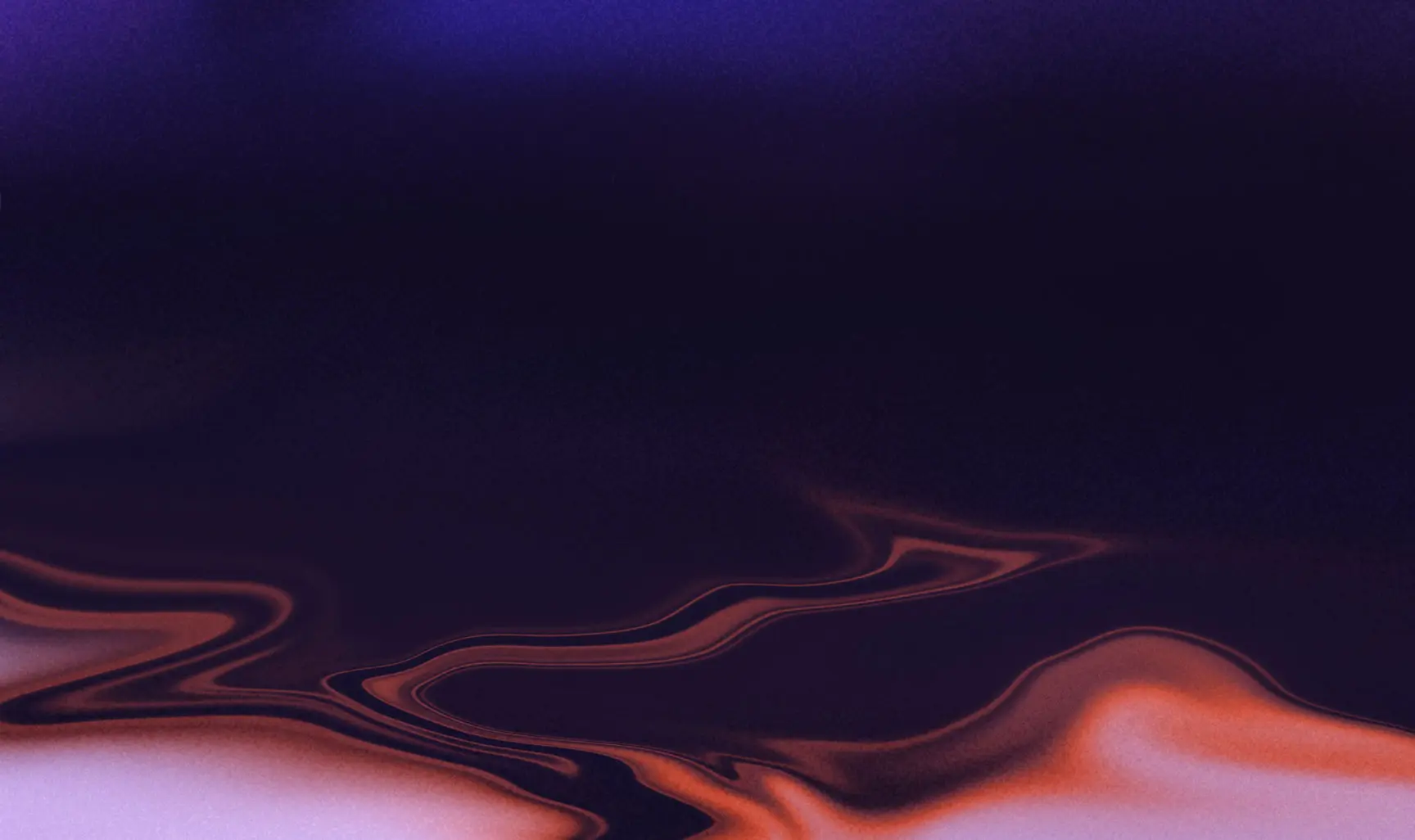
Ask our expert a question
Department Manager
Mandatory field
When you submit this form, our specialist will be in touch with you by email or telephone. By submitting the form you accept our privacy statement.