Etteplan Supports LiNA Medical in Production Improvement in Poland
LiNA Medical, a Danish company specialized in innovative medical devices, recently collaborated with the Etteplan team in the Netherlands and Poland to optimize production at their Polish factory at Poznań. It was a fruitful partnership that yielded valuable insights.
Through Etteplan's office in Poland, LiNA Medical connected with Etteplan Netherlands six months ago, seeking a solution to improve production at their Polish factory. They initially thought of an automation solution. To better understand the challenge, Etteplan invited LiNA to an LCIA workshop at their Son office. LiNA selected two technical writers to attend. There, they discovered the added value of LCIA and how this could support optimization of production within their production facility.
Subsequently, two Etteplan experts, supported by LiNA's product-responsible technical writers, conducted a Gemba Walk on site at the factory. This direct observation of the production processes in the cleanroom revealed inefficiencies, opportunities for innovations, and areas for improvement. "When you work a certain way every day, you become 'blind' to possible optimizations," said Bram Schreuders, Lean expert at Etteplan.
Production line as the leading principle
A key focus area was that the production line should determine how many people are needed, not the other way around. "In the current situation, the available production workforce determines how the line is set up," Geert Wondergem, System Architect at Etteplan, explained. "This creates daily variation in workflow and activities, which leads to a high risk of errors, rework and other challenges." Additionally, by working based on 'one piece flow', the processes can be better aligned, buffers eliminated, and nothing takes up unnecessary space from the moment an item enters the production line until it is completed.
A different way of working also requires a shift in mindset, something that needs to gradually become ingrained in the daily process. Fortunately, there is a great willingness at LiNA Medical to work and optimize in this way. This also requires adjustments at the organizational level. Working according to Lean principles requires commitment to continuously stay sharp on improvement points and this way of working.
The optimized working method creates calmness and clarity, and reduces the chance of production errors. Onboarding new employees also becomes easier. During the Gemba Walk at LiNA, the Etteplan experts were able to directly test their recommendations through an experiment on the production line. The changes enabled employees to quickly witness the advantages in the assembly procedure. This led them to embrace the suggestions and recognize the promising opportunities the modifications presented.
Bram tips: "Focus on one area at a time for maximum productivity gain"
The collaboration between the Polish and Dutch Etteplan colleagues was crucial. "It is important to share knowledge and learn from each other across different countries," Geert emphasized. "This way, we can continue to help our clients make their production processes more efficient and smarter."
The Etteplan experts are ready to support LiNA Medical remotely in the further optimization of their production processes. "With videos and photos, we can provide input and advice if desired," said Geert. "Step by step, we can continue to increase productivity in this way."
When asked for a tip for other manufacturing companies looking to optimize their production and considering a Gemba Walk, Bram advises: "Focus on one product, one process or one production line at a time. Optimize that and then move on to the next."
"Focus on one product, one process or one production line at a time. Optimize that and then move on to the next."
Bram Schreuders
Lean expert
A Gemba Walk offers production plants the opportunity to quickly evaluate the current way of working. Improvements might be implemented with relatively small investments, to easily reduce (time) waste or make other improvements. Experiments for example offer possiblities to execute a broader test of changing the way of working. With this approach, Etteplan can continue to inspire clients to challenge the status quo and achieve meaningful progress.
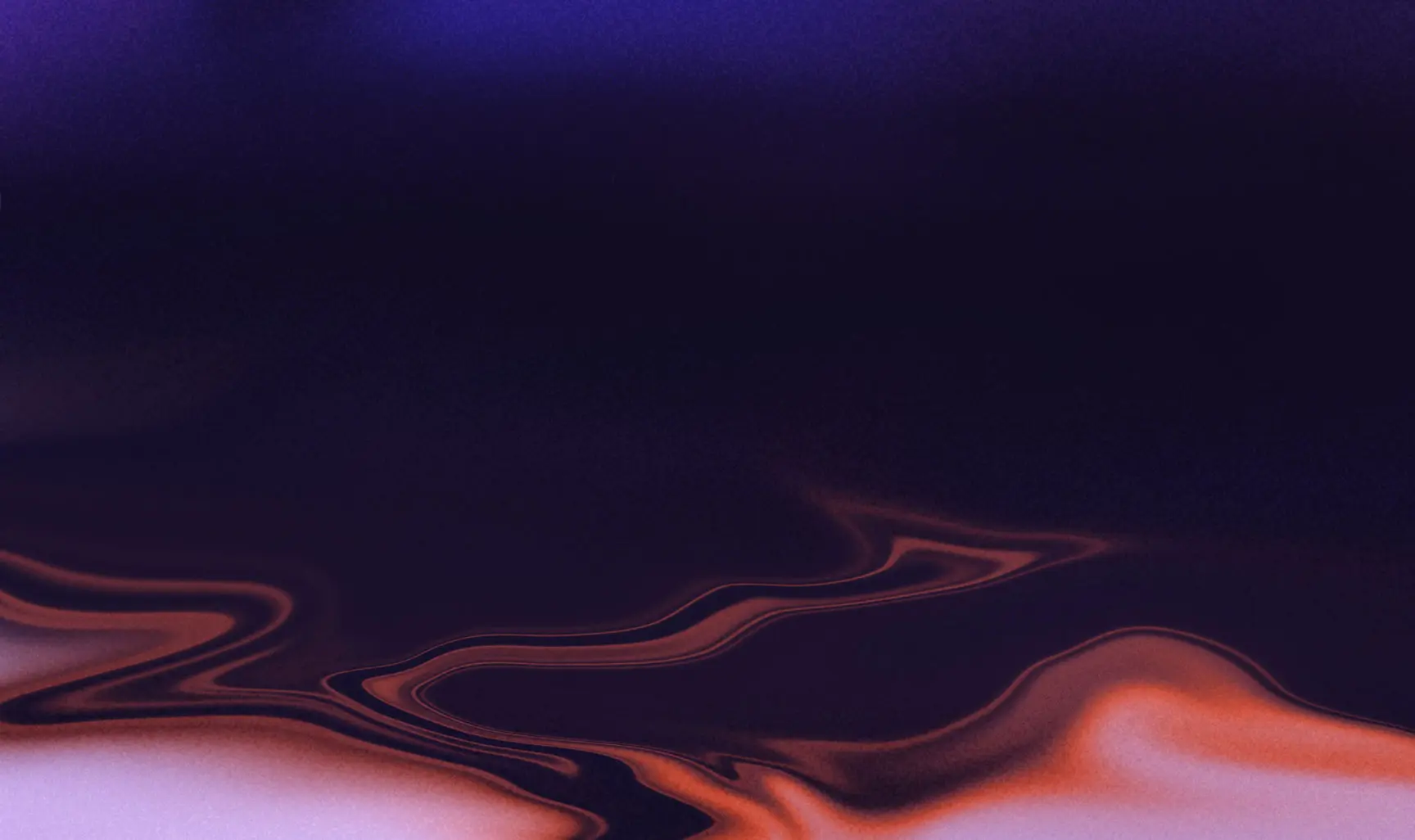
Ask our expert a question
Business Developer
Mandatory field
When you submit this form, our specialist will be in touch with you by email or telephone. By submitting the form you accept our privacy statement.