
Additive Manufacturing Design for Wärtsilä
Wärtsilä was willing to redesign their valve springs press tools by having a lighter structure made by additive manufacturing. The initial “standard design” was machined and welded, but there were fears that it would not withstand the spring forces of over 30 kN generated during use. Wärtsilä involved Etteplan to co-design and rethink the manually operated pressing tool for mounting cylinder head valves.
Four potential metals were considered for the final additive manufactured component, and design objectives included restrictions on manufacturing cost and material usage. The customer also wanted to understand how quickly this type of engineering and design task could be completed.

Simulation-driven design approach
To tackle this project, Etteplan assembled a team that included experts in AM production, AM design, topology optimization and print process simulation. The design workflow started with definition of available design space, boundary conditions and maximum potential loads that the tool would be exposed to during operation.
Altair OptiStruct and SolidThinking Inspire software were used to run topology optimization and FEM analyses for design concept generation. Inspire PolyNURBS were used to generate smooth CAD surfaces over the topology optimized results while allowing the organic features of the design to be maintained. OptiStruct was then used for performance evaluation of the final component design, and Additive Works Amphyon software, part of the Altair Partner Alliance (APA), was utilized to simulate the print process to ensure that the component was printable and that maximum distortion levels were within reason.

Benefits
Etteplan was able to create a pressing tool design that was ready to be printed within one week from when the project starting data was frozen. The topology optimized design met both the cost and material usage targets. Additionally, care was taken so that the design was self-supporting, which further reduces manufacturing costs by eliminating material waste and minimizing post-processing costs.
Keys to success
Etteplan’s final design of the pressing tool for mounting cylinder head valves met and exceeded all of Wärtsilä’s initial AM design objectives. The fast turnaround in this project was made possible by assembling a team of experts who used topology optimization to eliminate excess material usage in a self-supporting design and print process simulation to guarantee that it could be successfully manufactured.

Related reference cases
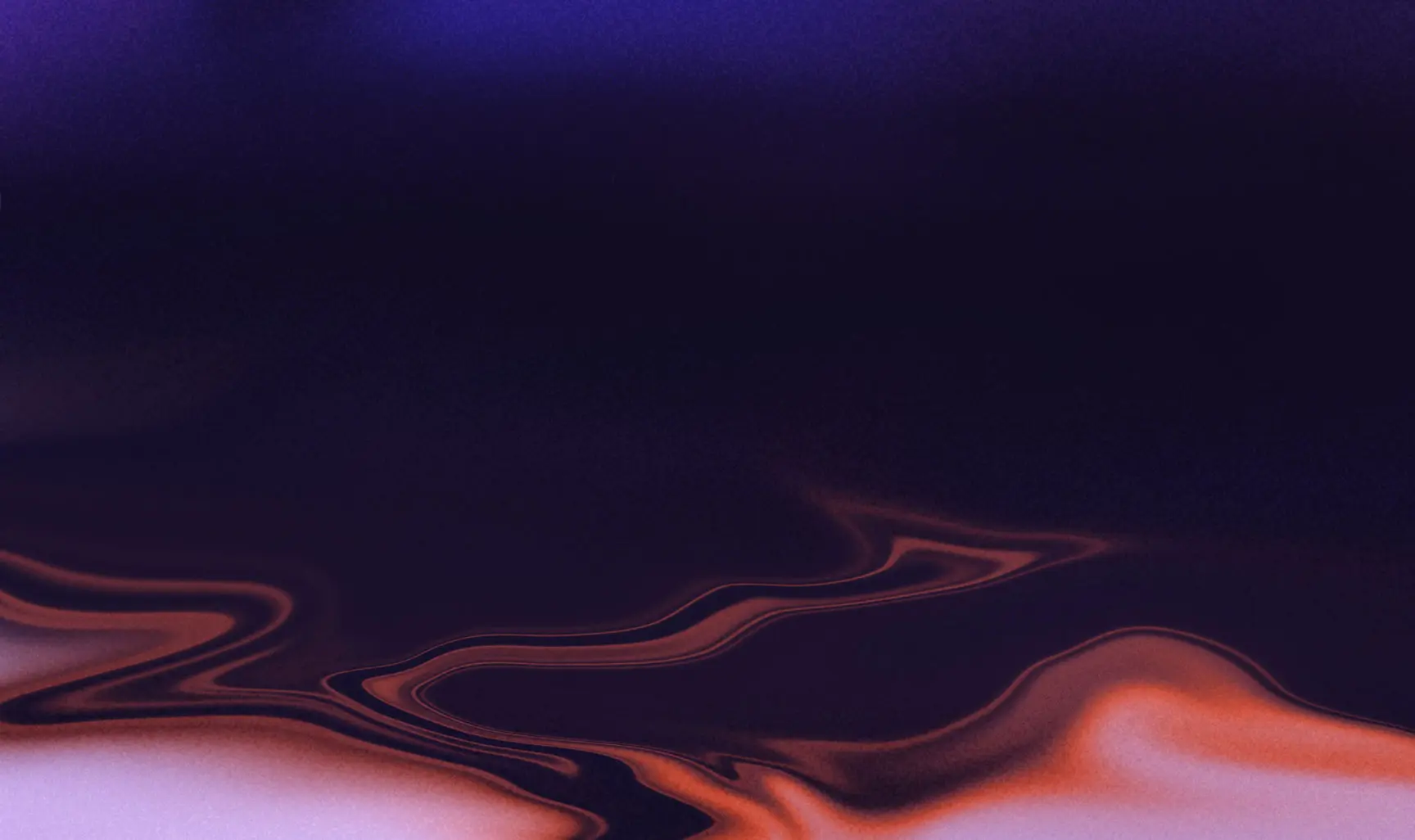
Ask our expert a question

Department Manager, AMO
Mandatory field
When you submit this form, our specialist will be in touch with you by email or telephone. By submitting the form you accept our privacy statement.