
The Five Biggest Challenges in Assembly Processes and How to Recognize Them
In the world of manufacturing, assembly processes are a crucial part of the overall production chain. These processes, which involve combining various components into a finished product, are essential for the efficiency and quality of the final products. As with any complex operation, there are various challenges that can affect the effectiveness of assembly processes. In this blog, we will discuss the five biggest challenges that companies face and how to recognize them. By identifying these challenges early on, you can take the necessary steps to address them and optimize your assembly processes.
1. Quality Issues
Quality issues are one of the most concerning challenges in assembly processes. Defective products or inconsistencies can lead to customer dissatisfaction and significant costs due to recalls and replacements.
Monitor defect rates
Customer feedback
Internal audits
How to Recognize:
- Monitor defect rates: Track defect rates throughout the production cycle.
- Customer feedback: Listen to complaints and suggestions from customers regarding product quality.
- Internal audits: Conduct regular quality checks and inspections to identify any issues early on.
An example: A consumer electronics manufacturer discovered that a significant percentage of their products were defective. By implementing thorough quality inspections, they were able to pinpoint the causes of the defects and improve their production processes.
2. Time Pressure
In many assembly environments, time plays a critical role. The pressure to deliver quickly can lead to errors and reduced product quality.
Measure lead times
Evaluate team stress
Complaints about insufficient time
How to Recognize:
- Measure lead times: Analyze the lead time of assembly processes to identify bottlenecks.
- Evaluate team stress: Talk to employees about their workload and their perception of time pressure.
- Complaints about insufficient time: Watch for signs of stress or burnout among employees.
An example: An automobile manufacturer noticed that their assembly teams often faced immense pressure to meet deadlines, resulting in an increase in errors. By revising their scheduling processes, they were able to create a better balance between speed and quality.
3. Ergonomic challenges
Ergonomics play an important role in the effectiveness of assembly processes. Poor workplace design can lead to injuries and fatigue among employees, affecting productivity.
Employee observations
Employee feedback
Increase in absenteeism
How to Recognize:
- Employee observations: Observe how employees perform their tasks and whether they appear uncomfortable.
- Employee feedback: Ask employees about any physical discomfort they experience during their work.
- Increase in absenteeism: Track statistics related to absenteeism and injuries associated with ergonomics.
An example: A factory that relied on manual assembly found that many employees frequently complained of back pain. By redesigning workstations and providing ergonomic tools, they were able to significantly improve working conditions.
4. Communication Issues
Effective communication is essential for a smooth assembly process. Poor communication can lead to misunderstandings and delays.
Conflicts within the team
Delays due to unclear instructions
Ineffective meetings
How to Recognize:
- Conflicts within the team: Monitor for frequent misunderstandings or conflicts among team members.
- Delays due to unclear instructions: Analyze the causes of delays and determine if they stem from unclear instructions.
- Ineffective meetings: Assess whether team meetings genuinely contribute to problem-solving or are merely time-wasting.
An example: A company that collaborated with multiple teams found that unclear instructions often led to errors in assembly. By establishing clear communication lines and protocols, they were able to improve efficiency.
5. Labor shortages
A shortage of labor can significantly impact assembly processes. This shortage often leads to increased workloads for existing employees, which can affect both productivity and the quality of output. In a time when demand for products continues to rise, it is essential for companies to find innovative solutions to compensate for labor shortages.
High workload
Difficulty finding skilled workers
Increase in overtime
How to Recognize:
- High workload: Observe whether employees are overwhelmed and struggling to complete their tasks.
- Difficulty finding skilled workers: Track statistics on employee turnover and challenges in recruiting new staff.
- Increase in overtime: Pay attention to the frequency of overtime and its effects on employee satisfaction.
An example: An electronics manufacturer facing labor shortages decided to integrate LCIA solutions into their assembly processes. By using smart technologies and improving the layout of the production line, they were able to increase production capacity without the need for additional staff. This led to a better work-life balance for their employees and an improvement in overall product quality.
The Role of LCIA
Low-Cost Intelligent Automation provides companies with the opportunity to enhance the efficiency of their assembly processes with less reliance on labor. By implementing smart, cost-effective automation solutions, companies can automate repetitive and time-consuming tasks, allowing employees to focus on more complex and valuable work. This not only helps increase productivity but also alleviates the workload for staff.
Additionally, with this focus on processes where operators are central, companies can easily train individuals without specific technical backgrounds and those distanced from the labor market to perform their tasks on the production line. This not only increases diversity within the team but also expands the potential available workforce.
Conclusion
Recognizing the five biggest challenges in assembly processes is crucial for optimizing production and ensuring the quality of final products. By addressing quality issues, time pressure, ergonomic challenges, communication problems, and labor shortages, companies can take proactive measures to tackle these issues. Take the time to evaluate these challenges in your own assembly processes and take the first steps toward improvement and success.
Take the First Step Toward Optimization
Do you want to improve your assembly processes and address the challenges you face? Contact us today for a no-obligation consultation. Our team of experts is ready to help you with customized solutions that fit your business needs. Together, we can elevate your assembly processes to the next level!
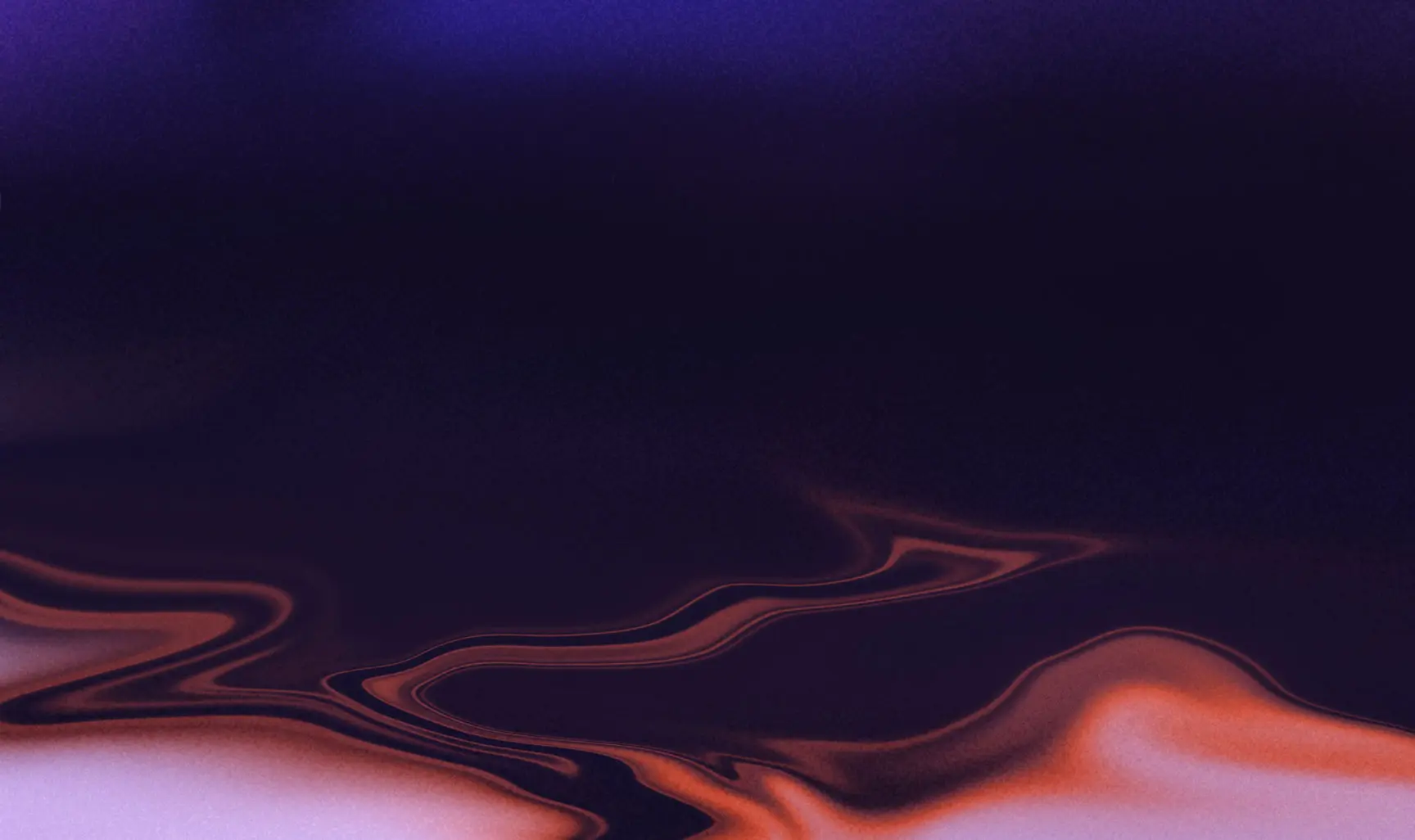
Ask our expert a question
On-Site engineering Director
Mandatory field
When you submit this form, our specialist will be in touch with you by email or telephone. By submitting the form you accept our privacy statement.